Why Automating Material Movement Is the First Step Toward a Smarter Warehouse
- John Stikes
- Apr 8
- 2 min read
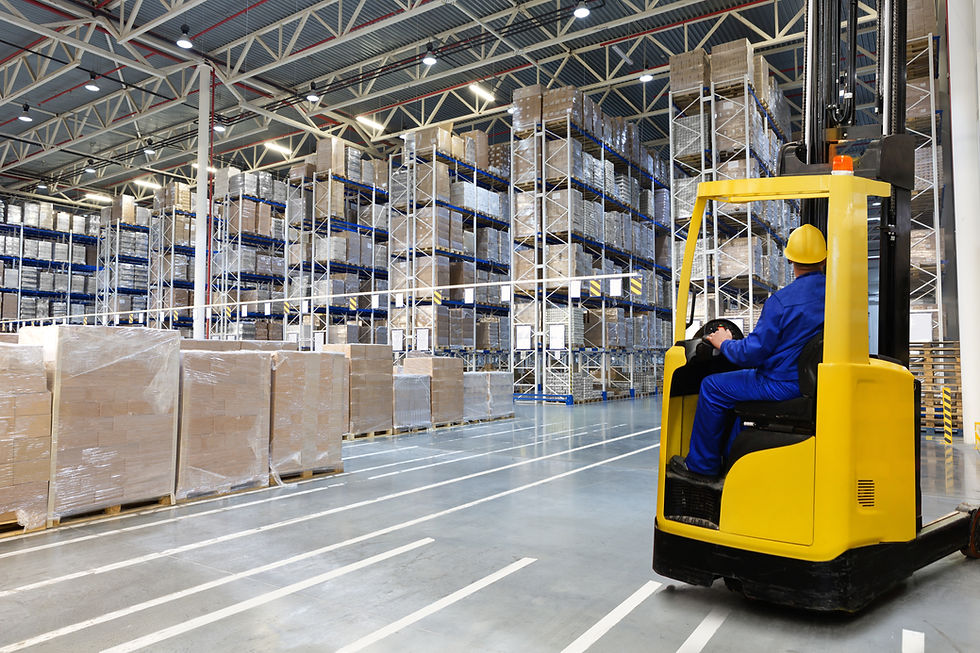
When most people think of warehouse automation, they picture a fully autonomous facility buzzing with robots and software-controlled systems. But the path to that future doesn't happen overnight—it starts with smart, strategic steps. One of the most impactful first moves? Automating material movement.
Why Start with Material Movement?
Material transport—moving pallets, totes, bins, and boxes—is one of the most time-consuming and labor-intensive processes in a facility. It also typically carries high indirect labor costs, especially when workers are walking product from point A to B instead of focusing on high-value tasks like picking, packing, or equipment operation.
By automating these repetitive and non-value-added movements, businesses can start unlocking serious efficiency gains without overhauling their entire operation.
An Iterative Approach Lowers Risk and Maximizes ROI
Jumping into full automation can feel risky—especially for small and mid-sized businesses. That’s why an incremental, targeted approach makes more sense. Automating material movement is often the best starting point because it:
Targets high-labor, low-skill tasks that offer quick returns.
Reduces operational strain without disrupting core processes.
Sets the foundation for future automation like robotic picking or automated storage systems.
This step-by-step method helps companies identify the areas with the highest ROI and lowest risk, allowing them to scale with confidence.
Build Smart—Not Just Fast
One of the biggest mistakes companies make in automation is treating it like a one-time install instead of an evolving system. That’s why it’s critical to work with an integration partner who understands how all the moving pieces fit together—from software to mobile robotics, conveyors to sensors.
At Approach Automation, we specialize in helping companies navigate this journey. Whether you’re looking to reduce indirect labor, improve material flow, or future-proof your facility, we help you design automation projects that scale with your business and adapt to change.
Understand the Full Cost Picture
One often-overlooked part of automation planning is understanding how projects blend capital expenses (CapEx) and operating expenses (OpEx). Some automation solutions require significant upfront investment, while others are subscription-based or structured as managed services.
To make smart decisions, businesses need to look at both sides of the cost equation. By evaluating capital and variable costs together, companies can:
Make informed budgeting decisions.
Plan phased implementations that balance investment with ROI.
Gain clarity on total cost of ownership and long-term value.
Labor Cost vs. Automation Investment
Many automation solutions—such as autonomous mobile robots (AMRs) or cleaning robots—cost significantly less than a full-time hourly employee when calculated over their useful life. By shifting routine material movement to automation, companies can redeploy human labor to revenue-generating tasks like production, quality control, and customer service—where humans thrive and businesses grow.
Approach Automation works with clients to develop a holistic automation strategy that factors in both CapEx and OpEx, ensuring your solution aligns with your operational and financial goals.
Start Small. Think Big. Move Smart.
Automating material movement isn't just a fix—it’s a foothold in your digital transformation. It’s about working smarter today while building a more resilient, scalable, and efficient warehouse for tomorrow.
Want to take the first step? Let’s talk about how Approach Automation can help you move smarter.